Challenges Facing the Manufacturing Industry
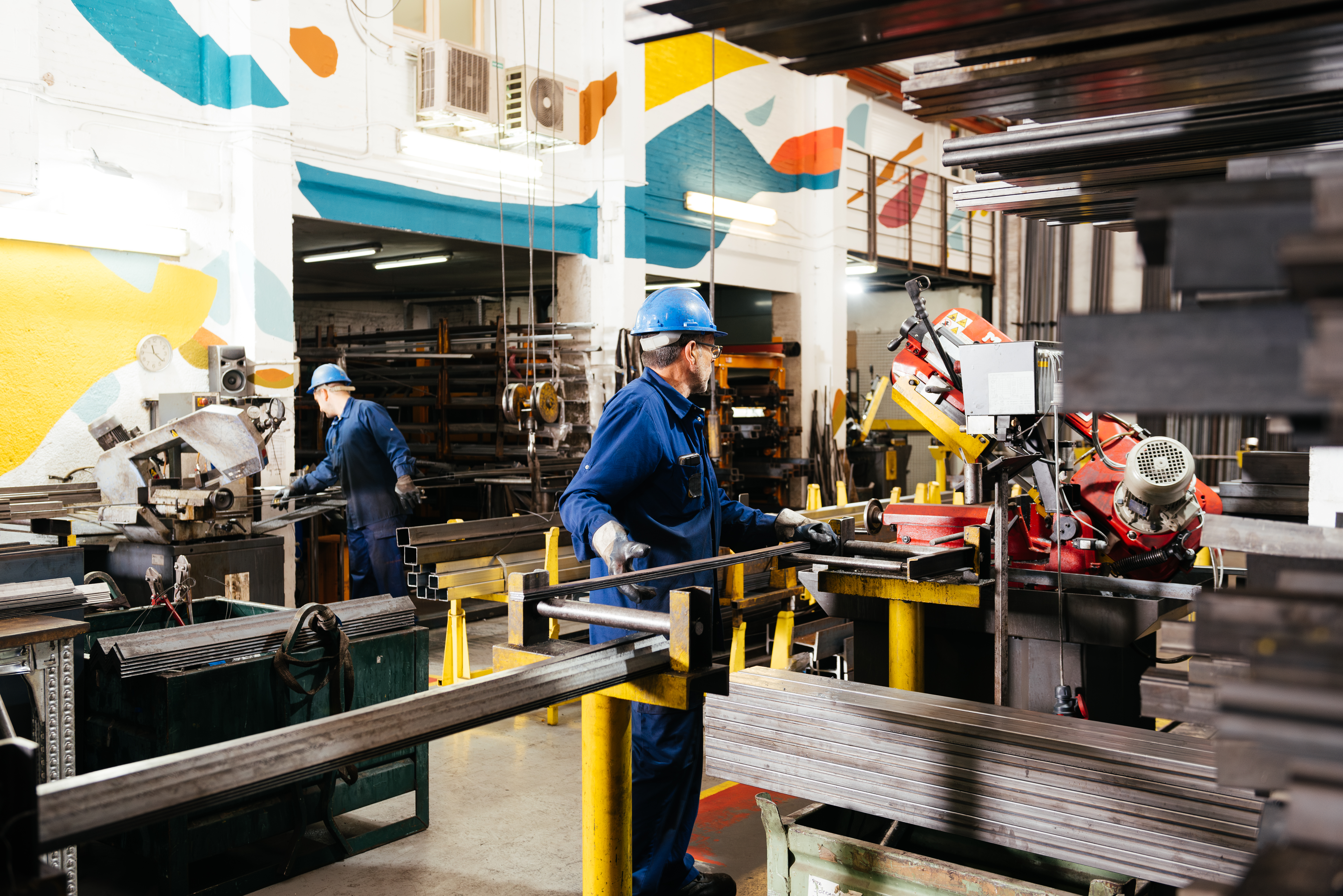
Table of Contents
Challenges Facing the Manufacturing Industry
December 4, 2024
The manufacturing industry is multifaceted and requires deep industry expertise, adaptability, and competitiveness. In this diverse and dynamic field, effective material sourcing, production planning, and distribution management are crucial for staying ahead, including maintaining productivity while transforming raw materials into finished products. The scale and complexity of this sector require business owners to remain agile while navigating numerous variables within and beyond their control.
As manufacturers strive to streamline their workflows, they must balance the intricacies of sourcing quality materials, optimizing production lines, and ensuring timely distribution. External and internal pressures, from fluctuating supply chain dynamics to the need for continuous innovation, can affect each step in this process.
As if the complexity of the manufacturing landscape wasn’t challenging enough, manufacturers also face a myriad of other challenges. Labor shortages pressure production schedules, while tighter deadlines demand greater efficiency at every workflow stage. The need for increased uptime and productivity is ever-present, requiring robust and reliable equipment to handle demanding tasks with minimal downtime. At the same time, aligning with eco-conscious strategies adds another layer of challenge as businesses seek to minimize their environmental impact without sacrificing performance or profitability.
Navigating these challenges demands a thorough understanding of the manufacturing workflow, from raw material acquisition to the delivery of finished goods, while identifying and addressing potential inefficiencies that could hinder business success. By tackling each of these pressing issues directly, manufacturers can strengthen their operational resilience and sustain a competitive edge in an ever-evolving industry.
Having identified the key challenges within the manufacturing industry, let's explore how these issues may impact your business.
Balancing a Reducing Workforce
According to the US Bureau of Labor Statistics, manufacturing's peak workforce was 19.6 million in June 1979. Since then, manufacturing employment has decreased by 35 percent, falling to 12.8 million from its all-time peak. Although consumer demand has increased, the number of individuals entering the manufacturing workforce has diminished. While this specific workforce has lessened, many in this industry are also reaching retirement age, meaning many experienced employees will soon leave, creating a gap in expertise that ultimately affects operational productivity and efficiency.
Recruitment in the manufacturing industry is difficult, particularly in a competitive job market, as employers struggle to find and train new workers to replace retirees. Effective knowledge transfer is crucial yet difficult to manage, as retiring workers’ expertise must be passed to younger employees. Training new hires and implementing these programs are costly and time-consuming, further complicating the issue.
In addition to a declining workforce, the demanding nature of manufacturing significantly impacts workers. Long hours, repetitive tasks, and strenuous activities lead to fatigue, chronic health issues, decreased job satisfaction, and higher turnover rates. These physical and mental demands affect not only individual workers but also overall productivity and morale within the industry.
All of these challenges stretch the manufacturer’s bandwidth while attempting to maintain demand requirements.
Overcoming Barriers to Productivity and Agility
Maintaining uptime and increased throughput is crucial in the manufacturing industry, as interruptions in material handling can cause significant delays and financial losses. Unplanned downtime significantly undermines productivity, and when combined with the industry's sensitivity to economic cycles and market fluctuations, it can critically impact a manufacturer’s bottom line.
Downtime can disrupt any operation. According to After The Fall: Cost, Causes, and Consequences of Unplanned Downtime, a study of over 100 global manufacturers found that 82% have experienced an average of two outages over the last several years. Additionally, 48% of respondents within the manufacturing industry see significant room for improvement in proactive asset management within their organizations.
Staying ahead of the curve demands proactive preparation and meticulous planning. Without this foresight, manufacturers risk falling behind more agile and innovative competitors, which can lead to a loss of competitiveness. Effective planning goes beyond best-laid plans; it requires anticipating even the smallest details that could derail your production goals. These insights include understanding how an operation’s assets support effective, productive, and reliable performance—particularly in sourcing equipment that precisely meets operational needs. Manufacturers must look beyond acquiring the best equipment for the job and focus on whether that investment will
Striving for Sustainability
The shift towards sustainable manufacturing has gained significant momentum in recent years and has become a central topic in business discussions. Alongside regulatory compliance and the recognition that eco-friendly practices are smart business, manufacturers must balance cost, quality, and performance to meet this growing trend. However, many find planning and implementing sustainability strategies both costly and complex, and they struggle to maintain consistent standards across their supply chains. Amid efforts to reduce their carbon footprint, manufacturers must also ensure operational efficiency to meet consumer demand.
In this context, manufacturers face various complex challenges as they strive to integrate sustainability into their operations. Adhering to stringent environmental regulations is crucial to avoid fines and protect the company's reputation, which demands ongoing vigilance and resource allocation. While sustainable practices often require significant upfront investments in energy-efficient machinery and eco-friendly materials, they offer substantial long-term savings through reduced energy consumption and waste.
The quest for sustainability extends throughout the supply chain, necessitating close collaboration with suppliers and investments in transparency to ensure eco-friendly practices are upheld. Balancing these efforts with operational efficiency is essential to meet consumer demand without compromising productivity, requiring manufacturers to optimize processes and leverage advanced technologies.
As consumer preference shifts towards sustainable products, effective marketing of these efforts can enhance brand loyalty and unlock new market opportunities. Additionally, embracing sustainability drives innovation, providing a competitive edge that attracts customers, investors, and talent committed to environmental responsibility.
By addressing these interconnected challenges, manufacturers can achieve their sustainability goals and strengthen their position in a rapidly evolving marketplace.
Driving Solutions, Building Partnerships
Are you feeling overwhelmed by the relentless demands of maintaining productivity and embracing new initiatives? At Linde Material Handling, we understand the complexities of balancing operational efficiency with sustainability and navigating a challenging workforce landscape. Our tailored solutions are designed to address these pressing issues and support your unique business needs. Partner with us to streamline your operations, enhance your sustainability efforts, and discover how Linde Material Handling can help you stay ahead in an ever-evolving industry.
Let’s keep the world moving together.
Related Insights
Find a Dealer